By Florence Collins
A long-term clinical lab study lasting over 10 years showed that more than 60% of all mistakes in the stat lab (the lab that receives high priority samples) can be attributed to the pre-analytical phase. This figure has not changed much from 1997 to 2007,1, 2 despite advances in the technology.
With higher numbers of samples to process, lab managers need ever higher sample throughput and error-free connection to the sample ID. Many solutions on the market can scan barcodes on test tubes, but they are all limited by an age-old problem: the dead time between loading the tubes, reading the tubes and handling the errors. The decoupling of tube loading and barcode reading from error handling disrupts an otherwise smooth lab workflow and introduces multiple sources of human error.
Instant error handling
The Fluent ID tube 1D barcode scanning module gives immediate feedback to the operator, making tube loading and reading a single fluid action, thereby reducing the impact of human error.
Whistle while you work
Prior to the introduction of Fluent ID, lab operators were forced to either scan test tubes manually, which takes time and is error-prone, or, with an automated scanning system, operators could load all the tubes on the robot and… simply wait and watch. Although the system handled the reading of barcodes, operators still needed to return to the machine after all the tubes had been read to check if there were reading errors -- such as a missing tube, or a missing, unreadable, or duplicate barcode.
Fluent ID reads the barcodes while you load the tubes, so you get immediate feedback on the success of the reading process. In fact, it is simultaneous. The operators' hands are still on the tube rack when a red blinking light in front of the rack in question notifies them of the error. The immediate error notification also appears on the Fluent touch screen display.
Fluent ID fits any workflow and its ability to instruct operators what to do while they are loading the tubes is the key to improving workflows and reducing errors. The traditional process is more time-consuming and less secure, since the operator must try to locate the problem tubes during an analysis that takes place after loading and scanning of all the tubes. In the conventional scenario, the entire process takes longer, the operator might remove the wrong tube from the rack, and the subsequent error may be difficult to identify and act upon.
Born to run
Fluent ID solves all these challenges, as well as the important matter of capacity. Tecan paid special attention to ensuring an easy workflow when working with large numbers of samples. The Fluent system can accommodate up to 192 tubes in the format of 6 racks containing 32 tubes each. Lab managers will be delighted to know that the Fluent ID can handle multiple batches of tubes in a continuous run, thanks to its parallel processing capabilities. You do not need four Fluent ID modules to manage 768 tubes. A single Fluent ID module would be sufficient.
The system can handle parallel actions like scanning tubes and transferring liquid from other tubes at the same time. Therefore, operators can remove processed tubes, and load a new batch while processing is going on.
Rock solid performance
Automation is best when the need for maintenance, calibration and service is minimal. Fluent ID is a laser scanning reading system with no moving parts and is therefore extremely robust. This, combined with multiple checks for each barcode read and checksum controls means that there are no misreads due to mechanical issues.
Labeled tubes from another lab may not meet your high standards and the labels may have been applied at an inconvenient angle. No need to worry – Fluent ID is forgiving. The system applies image reconstruction technology, taking two incomplete barcode images and piecing them together. All you need to do is orient the tubes so that the label faces to the left and Fluent ID will take care of the rest.
Operator guidance with colorful lights
For operators, ease of use is better than ever before. Colored lights placed directly in front of the loaded tube rack indicate read success or read errors. The system can also specify the rack that belongs in each grid by providing a colored light to match a rack’s color code.
From a regulatory standpoint, Fluent ID includes important data security and protection measures. If a rack is partially pulled out from the worktable, you must pull it out fully to re-read it. You can export barcodes to your LIMS, via a CSV file, with all errors tracked, including connection to the operator ID. User management is fully supported by the Fluent platform. The system is therefore ready to be used according to 21 CFR Part 11 guidelines for submission of electronic records.
Fast
If a lab operator spends 3 minutes a day, twice a day waiting for tubes to scan that adds up to more than half a working week over the course of a year. Add to that the cost of human errors. Today, lab time and resources are precious, and human error is the main source of errors in sample processing. Fluent ID makes your lab work flow more smoothly than ever before, and provides ultimate scanning confidence.
References
- Mistakes in a stat laboratory: types and frequency. Plebani M and Carraro P. Clin. Chem. 43 (8), 1997. https://academic.oup.com/clinchem/article/43/8/1348/5641004
- Errors in a Stat Laboratory: Types and Frequencies 10 Years Later. Plebani M and Carraro P. Clin. Chem.53 (7), 2007. https://academic.oup.com/clinchem/article/53/7/1338/5627526
Fluent is a Class 2 Laser Product when equipped with Fluent ID option.
Research use only.
About the author
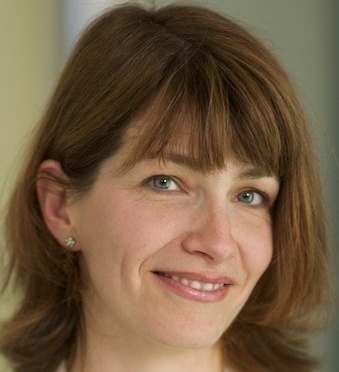
Florence Collins
Florence Collins is a product manager at Tecan Switzerland. She holds a master's degree in Agronomy. She joined Tecan Systems in 2000 as key account manager in California and moved to Tecan’s head office as product manager in 2006.