By Severin Heynen
As labs face tighter profit margins and the need to minimize cost of goods, there is increasing pressure to implement more efficient and responsive mechanisms for procurement and inventory management. A large proportion of annual spend goes towards consumables like disposable pipette tips, microplates and kits. Procurement strategies based on lean and ‘just-in-time’ principles can improve cost-efficiency by reducing overhead and warehousing expenses. However, this often comes with a significant risk: without enough data about both availability of consumables and what you have in stock, you could run into costly unexpected out-of-stock scenarios. Here are three essential questions to ask when looking to reduce the risks of creating leaner, ‘just-in-time’ procurement processes.
New software tools for automatic collection, analysis and visualization of consumables usage data can help de-risk ‘just-in-time’ inventory control, while increasing responsiveness and transparency in the procurement process.
1. Do you have enough data about usage of lab supplies?
The success of lean strategies and ‘just-in-time’ solutions depends on having quality information when you need it. Accurately balancing stock against requirements can be especially important when working with reagents and consumables that can unexpectedly increase in demand.
More data about systems and consumables usage can be key to spotting important trends and taking appropriate action quickly. In addition to monitoring consumption in real-time, there is also a lot to be gained from mining archived usage data. For example, in the clinical setting, sample numbers and particular tests may spike dramatically during cold-and-flu season. However, the magnitude of these trends on consumable and equipment usage may only become evident after looking at the historical data.
Chances are that your organization already has a virtual goldmine of untapped usage data. The problem is that most of it is may be lurking in out-of-date spreadsheets or instrument log files that are hard to access in a timely matter.
2. Is your procurement process responsive enough?
With ‘just-in-time’ and other lean approaches, your lab stands to profit by responding more quickly and effectively to changing needs. However, the reality of these methodologies does not always live up to expectation, and usually the underlying reason is that there simply is not enough reliable information available when you need it to support good decision-making.
To make ‘just-in-time’ inventory control work, you need to be able to make the right decision quickly and adjust inventory as needed. Usage data can help highlight opportunities to de-risk sourcing, and improve service. For example, when a particular lab is increasing throughput of a test that relies on a consumable, it may make sense to increase stock levels of this part to allow testing to proceed uninterrupted. Likewise, when usage analysis correlates unusually high instrument downtimes with delays in shipment of lab supplies from a foreign vendor, it may be time to qualify alternative local suppliers.
The bottom line is that real-time and historical data about the usage of instruments, robotics and lab supplies are essential for responsive decision-making. Without accurate and timely information, ‘just-in-time’ approaches can become too risky.
3. Is there enough transparency and flexibility?
Lack of procurement data visibility and transparency across an organization can lead to bottlenecks and uninformed decisions that undermine ‘just-in-time’ solutions. Having reliable usage data is a good start, but equally important are easy data access and effective analytics that help you interpret the data and adjust accordingly. In many cases different departments and functions of an organization must collaborate to assist in the procurement process.
Some processes that make sense from a financial standpoint might look counterintuitive until they are analyzed from multiple perspectives. To the procurement officer, for example, a bulk sale price may appear to offer a big cost savings, while from the warehousing perspective multiple small orders at a slightly higher price would reduce inventory costs. Only when both functions are able to review the data and correlate their results does it become apparent which of the two scenarios will yield a net benefit in the long run.
Timely data is key to ensuring benefits of lean strategies outweigh risks
Lean strategies for inventory control can save you substantial money and render your organization more agile, but only if they are based on accurate usage data. Fortunately, there are emerging tools that can help procurement teams gather, analyze, visualize and share the necessary data. When looking for solutions, real-time reporting, transparency and connectivity are key.
To find out more about new tools and solutions for more responsive and cost-efficient procurement, watch our tutorial.
About the author
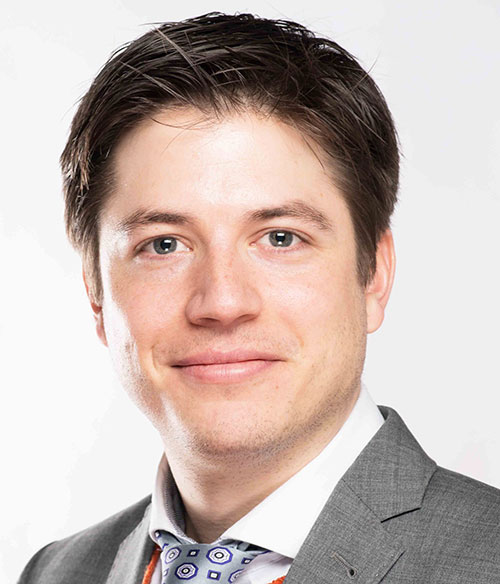
Dr Severin Heynen
Dr. Severin Heynen joined Tecan in 2015 as a product manager responsible for the disposable tip consumables. In his PhD studies at the University of Zurich, he mainly used biochemical and molecular biology techniques to study the mechanisms of retinal degenerative diseases.