By Andreas Scheidegger
Introducing a new in-vitro diagnostics (IVD) lab automation solution can add an entirely new dimension to your existing product portfolio and business. Launching a complete system that provides harmony between chemistry and assay workflow, instrumentation, software analysis and reporting is a complex endeavor that demands careful planning and execution.
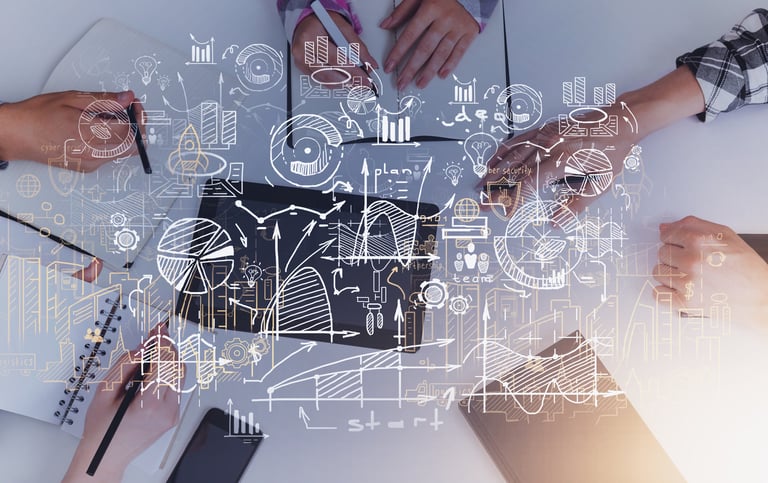
Commercialization of new diagnostic tests often requires a contract manufacturer that can support instrument development.
A growing and aging population and increasing public demand for healthcare goods and individualized services are all contributing to rising health care expenditures. For instance, modern precision medicines such as RNA and gene therapies in the fight against cancer are increasingly ramping up but have yet to provide their full potential around affordability and efficacy. In parallel, diagnostic laboratories are asked to improve reproducibility and precision—and reduce human handling and instrumentation errors—all while facing shortages of skilled staff.
Meeting these market challenges and trends, although daunting, presents fantastic opportunities for an IVD solution supplier to introduce a market-changing automation system—but only if the perspectives of end users and other key stakeholders are fully understood and accounted for in the design. Unfortunately, too many IVD companies are too often driven by “time to market” when it comes to system development, and by doing so, overlook other important factors that are essential for a successful IVD product launch.
Not taking adequate time for planning and development carries a high probability of suppressing key aspects, such as outlining a winning go-to market strategy, properly addressing cost of ownership, and ensuring that assay integrity and usability needs are fully met. Progressing overly fast carries an inherent risk of insufficiently addressing important market and end user research, regulatory considerations, and launch and post-launch aspects, resulting in an IVD lab automation product or service that clinicians and hospitals won’t bring forward. Increased cost pressure and shortage of skilled staff in hospitals, clinics or test facilities are real issues that require adequate attention. Factors such as system uptime management and ease-of-use must be considered as part of your IVD instrument development plan and delivered completely transparently to the end users.
Does your IVD automation system solve the right problems?
Prior to developing a new lab automation product or IVD system, take the time to gain a comprehensive understanding of how your envisioned product is going to help the lab and its users. That involves:
- studying the lab technician and the lab manager user needs
- carefully listening to and observing users in their working environment
- conducting customer surveys
Distill and translate the learnings into simple features and requirement sets for the development teams, and assemble go-to-market strategy for your cutting-edge system. Test your hypotheses by involving key opinion leaders early. Prove to yourself that the market and clientele truly exist and that reimbursement plans will work for your clients.
Real-world examples of challenges in IVD solutions development
Here are two typical scenarios that illustrate how the process of automating IVD workflows can turn up new and sometimes unexpected challenges for developers:
-
On-board reagent stability
In a manual process, a reagent might remain completely stable at room temperature on a lab bench over a 6-8 hour workday. But if the goal of an automated solution is to run 24/7 utilizing reagents, then those reagents may may not provide the needed on-system stability over that period unless active on-deck cooling or maintained storage conditions are built-in.
-
Loading and unloading an automated system with reagent vials
Unpacking a box of 12 individual small reagent vials and placing them on the lab bench makes sense for a manual process. However, the same kit setup for an automated system processing several hundred samples a day might be challenging for the same technician—both in terms of keeping track of the reagents and keeping up with the instrument speed. There may be a number of different possible solutions to this problem, ranging from integrating specifically designed loading trays to implementing changes on the package manufacturing side.
Often in cases such as these, it is a matter of finding an acceptable balance between several competing factors. These trade-off discussions are worthwhile and absolutely necessary to help you develop a more effective development and and market strategy. The earlier in the development process you can have these conversations the better.
User profiling is important
Considering your design from the end user’s perspective is an essential step in good product design. This means investing time in profiling the different types of users who are likely to interact with the system, as well as outlining the needs of other relevant stakeholders such as the lab director, procurement officer and quality manager.
For each profile, outline the person’s main goals, motivations, needs and day-to-day workflows in the lab. How does he or she interact with similar products in the market? Do existing solutions address all of the pain points already? Once that is mapped and understood then converting that gained insight into winning product requirements becomes simpler and provides valuable context for the entire development team.
Outline cost of ownership
From the perspective of the lab manager or procurement officer, the direct instrumentation costs are only part of the equation when it comes to making a purchasing decision. Consider the bottom-line impact that owning your system will have for clinics and labs on business operations, not just the initial product purchase. Then, if needed, outline practical steps for how to mitigate that impact. Besides obvious considerations, such as cost of goods, system price point and amortization plans, here are few additional aspects that may be of use:
- Built-in tools to help users and lab managers maximize system uptime
- Transparency of consumables usage and trend management
- Fleet or installed-base management
- Obsolescence planning and life cycle management in general
- Current and changing regulatory requirements that affect how your system usage is monitored, documented and audited
Plan for more uptime
If your system is being designed for a clinical lab or other high-demand setting, maximizing system uptime is a must. While it may seem like a costly exercise to thoroughly model system usage patterns and then optimize your design accordingly, anything you can do to improve system uptime is likely to give your system a competitive edge over less cost-efficient solutions on the market.
To put it into perspective, a mere 2% increase in system uptime over a 40-hour work week for a period of seven years would increase system availability by as much as 280 hours in total. In a 24/7 environment, that same 2% increase would yield more than 1,000 additional hours of availability over the same period.
Avoid rushing to launch
Rushing system development projects bears the risk that the result may be a mere copy of what is already on the market, or not an acceptable product for the labs. Not only is it essential to understand new user requirements, but also to consider how an automated system might change the workflow or consumable procurement process of a clinic or lab. In the rush to market your product, the team may fail to address essential questions such as:
- What is the laboratory's motivation for changing their existing workflow and/or automated systems over to yours?
- How will a lab validate your solution? How much time and cost are they willing to absorb?
- Who needs to be trained on the system? What is their background?
- What scheduled service intervals do your clients need? What tools are provided for early indications for potential system failures?
- How does your offering help the lab to reduce cost per test (or cost per result) in a holistic approach?
- How can clients find your product, how will they evaluate it, and order your products?
- And there are many more…
Taking time to consider questions such as these, rather than rushing to launch, can uncover valuable insights that increase your chances of a successful design.
Prioritize user safety and assay performance
Last but not least, consider adequate safeguards—for process integrity, system security and end user safety. A properly designed system addresses critical aspects like biohazard disposal, potential cross contamination, and assay integrity in a transparent way to end users.
Delivering a winning complex system for the healthcare market is not an easy task by any means, but taking the needed time for planning, business modeling and selecting the right partner for consulting, development and production will pay off in the long haul.
Are you ready for your next lab automation project? Get a free copy of our self-assessment checklist here.
About the author

Andreas Scheidegger
Andreas Scheidegger, Head of Customer Solution Development, together with a team of commercial scientists, advises and guides OEM system partners from ideation to project start to ensure envisioned products meet end-user and market demands, compliance and regulatory aspects. Andi has been in the Life Science and Healthcare industry for more than 20 years, and provides a broad range of expertise from his various roles in commercial, business development and R&D program management.