Keywords:
By Claudio Bui
Everyone knows if you work harder and faster you’ll get done sooner, but then many are left wondering why they didn’t get to market first. It may seem simple, but when it comes to life science laboratory automation it’s not as easy as it seems.
The revenue potential for the first supplier to introduce new technology to market can be enormous. Timing is always vital, and with automated liquid handling, exceptional standards of quality are also essential. Your systems must meet rigorous regulatory requirements. They must deliver highly accurate and consistent results, time after time. Even with these stringent requirements, your customers are also concerned about maintaining a lower total cost of ownership. Delivering a system that satisfies all of these needs is indeed a challenging task. Read on to find out how a systematic approach to scoping your users’ requirements and evaluating project assumptions can simplify your development process and speed time-to-market.
Strategic development planning, not just speed, is essential to being first-to-market with automation solutions for the competitive molecular diagnostics industry
Think like your end-user
Users of automated liquid handling systems have different needs. Researchers dig deep. They are looking for the smallest, the least, the best, the unknown. They push performance specifications to the limits, and they need reproducibility to publish their findings. However, researchers are also cost-constrained by grant budget limitations.
In contrast, suppliers of in vitro diagnostic (IVD) tests need clear, unambiguous answers whenever and wherever the test is run. Is an indicator of disease present or not? Answers to their tests directly impact patients. They must uphold the most stringent regulatory requirements. In addition, the information IVD tests deliver has tremendous value, so IVD providers are often willing to pay a premium for an automated liquid handling platform that ensures the best results from their own products.
Finally, institutions that are designing laboratory-developed tests (LDTs) need the same clarity and certainty as for IVD tests, but they are generally not subject to the same extent of regulatory approval.
By establishing at the beginning of your project exactly who your target customer is and what they need, you can move through each phase of the project with very specific and well-defined objectives. Decisions will be guided by those objectives so that the project can move forward without unnecessary debate and delay.
Map out the course
Getting ahead of your competition goes beyond knowing what your users will do with their automated liquid handling systems. Just as the most successful racers know their course ahead of time, you can streamline your development by mapping the entire process step-by-step before you begin. There are two perspectives to map.
The first is the perspective of the sample. What is its journey from the point that it enters the instrument through to the end of the run? Is it barcoded? Is it manually moved by the user? Is it incubated?
The second perspective is that of the user. How will they interact with the instrument? What happens first? How does the instrument react? What options does the user have to respond? When these stories are defined at the beginning of a project, everyone on the development team understands the workflow and can contribute to successful integration of all of the system components.
Focus on the essentials
Delays resulting from the feature specification phase of laboratory automation development projects usually fall into two basic categories: too much or too little. Considering the needs of varying user types, the “right requirements” rarely means “every option.” New technology and new applications are exciting. It can be tempting to offer all possible capabilities. However, most users do not need every feature you can offer. In addition, each new functionality must be specified, designed, tested, and regulatory-approved. Thus, adding unnecessary features adds unnecessary complexity and unnecessary project delays. Incorporating ready-to-use liquid handling components can greatly minimize both the complexity and delays.
It can be equally tempting to constrain a new system to a very small set of features with the intention of launching sooner, only to find that the system can’t quite do what your users need it to do or your competitors have launched a more suitable product. Adding new requirements at the end of a project is very risky. When key functionality is excluded from the initial planning and added quickly at the end of a project, it is very difficult to work backwards to integrate it seamlessly with the initial system.
Going through the process of defining the journey of the sample through the system and the interaction of the customer with the instrument will help to clarify the optimal product requirements and simplify the development process.
.png?width=600&name=OEM-components-illustration-large%20(2).png)
Systematic evaluation of user and project requirements can help speed time-to-market.
Avoid common development traps
There are three common traps to avoid in planning a laboratory automation development project.
1. Too many requirements. One common development trap is starting with too many requirements. Each required element must be designed, tested, and integrated. A system with fewer requirements will be easier to verify and validate. A pre-assembled off-the-shelf liquid handling component can deliver multiple pre-validated performance requirements in a single unit, ready for integration into your system to facilitate a speedy product launch.
2. Underestimating effort. The second potential pitfall is underestimating the effort required to integrate all components into an automated liquid handling system. Everyone on the development team has unique mechanical, electrical, software, or applications expertise that contributes to a high-quality product. However, uniting all of those individual elements for a single coordinated development project can be difficult. The entire team must work as a coordinated unit to build a fully integrated system from the beginning.
3. Starting from scratch. The third signficant time-waster is to start everything from scratch. People who develop laboratory automation systems love to build things. However, it is important to recognize that building from scratch is not always the fastest route to completion. It is also not the best solution to meeting a wide range of stringent requirements for automated liquid handling. Using off-the-shelf OEM components can save time for the development team to focus on their own passions and areas of expertise. Judicious selection of high-performance, pre-validated, and ready-to-use components can simplify product design, facilitate regulatory approval, and significantly reduce project risk.
Using OEM components puts you ahead
Delivering an automated liquid handling platform that meets the performance, regulatory, and cost requirements for customers ranging from research to IVD is a challenging task. Careful attention to the unique needs of different types of users, the sample journey and customer interactions, and common pitfalls is vital to producing just the right product for your customers. In many cases, off-the-shelf OEM liquid handling components can can greatly simplify and streamline product development, project completion, and release to market. There can be only one first to market, and it should be you.
Watch the video
Watch this video to learn more about how you can reduce time-to-market with your next liquid handling instrument development project.
Keywords:
About the author
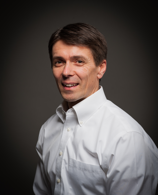
Claudio Bui
Claudio Bui is the Head of Product Concepts for the Partnering Business in the Components Marketing Team. The primary function of his team is to work closely with customers to develop new concepts and proposals based on a thorough analysis of their specific requirements. Claudio started at Tecan in 1990 in R&D developing Components and has been involved in the development of a number of small laboratory instruments. In 2005, he joined the Marketing team.