By Florence Collins
Scinomix, Inc., founded in 2001, creates customized solutions for labeling tubes, vials and plates in many life science applications. We took the chance to ask Nigel Malterer (CEO) and Jonathan King (Automation Software Engineer) at Scinomix about how automated barcode labeling solutions are helping to improve productivity, reduce errors and costs, and increase control over lab workflows.
Could you tell us how you are helping scientists to implement barcode labeling in lab automation?
Barcoding has become key to maintaining control over lab workflows
“One of our first customers was the Broad Institute in Boston that handles thousands of incoming samples a day in a 96-format rack of tubes. It was very tedious for their educated workforce to put on sticky labels, get them in the right place and orientation, and fully adhered. Getting the label square is one of the challenges, especially when the barcode has to be read by some sort of automation down the line. If the one-dimensional barcode down the tube is crooked then a lot of the legacy clinical systems cannot read the code and the tube is rejected. Introducing automation really helped them to improve labeling performance, free up time for their personnel, and reduce repetitive strain.”
“For many labs, including drug discovery labs, labeling samples is just part of the process and shouldn’t take up much space. So, a lot of automation solutions are benchtop size. Compact labeling systems suit the smaller labs that are not at a point where they can standardize and automate everything. They view automation as being the assistant. It’s like having another lab tech in the lab that is good at one thing – sticking labels on a tube. And users confirm that replacing trained personnel with labeling automation that simply sits in the corner of the lab and does its job has a short payback time.”
“Automation also provides a ready way of scaling up. With manual labeling, the only way to deal with more samples is to put more people in. With automation you can, for example, add on a system that can process tubes poured into a feeder. We have some Tecan customers who put Vacutainer™ vials into a hopper mechanism. The vials then get fed into the labeler and placed in the Tecan rack with the barcode in the correct orientation, ready to be placed directly into their Tecan lab automation system. So tedious manual work is replaced with repeatability and reliability.”
How are you collaborating with Tecan?
“We work with Tecan by providing either a fully automated labeler that pre-labels tubes or plates before they go into the Tecan system, or a piece of labeling automation that integrates with the Tecan system so that the labeling is done in real time. The tube is then delivered to our system by the Tecan Robotic Manipulator arm, the Tecan instrument having control over the automated labeler.”
How fast is the process of labeling and reading barcodes?
“An automated labeler can have a throughput of up to around 400 tubes/hour, in other words one tube every 9 seconds. A barcode can be read in less than a second, depending on code readability. In an automated labeling system, the tube is picked up and if the barcode doesn’t typically wrap around the tube, such as for Code 128, the tube is spun in less than a second and the code is read almost instantly. So this is hardly a bottleneck in the lab. The longest amount of time it takes is to pick the tube out of the rack, place it in the roller mechanism, clamp it and spin it.
How does labeling automation reduce error rates?
“Labeling systems that are well maintained have low error rates. And if you include confirmation steps, including reading the barcode after it has been printed and the label has been applied to the tube, then you increase the reliability even further. One way of reducing errors is by placing the tubes in an order based on algorithms or in an order specified by the customer. Specific checks can then be included to confirm that the label contains correct information and was applied correctly.”
“Newly developed techniques using OCR (Optical Character Reading) can also catch a lot of errors and help in checking the quality and correctness of labels as they are printed and applied to the tubes, followed by capturing an image that can be stored in a database for future reference.”
There are many barcode symbologies. Is Code 128 the way to go for clinical labs and drug development?
“A lot of the blood analysis systems do use Code 128. It’s a compact linear code and is the most reliable of the 1D codes. Ninety percent of what we print right now is the linear Code 128. We also see that some customers are moving towards 2D codes.”
What are the advantages and disadvantages of using 1D and 2D codes?
“A 2D code has an order of magnitude higher area efficiency compared to 1D. The redundancy in 2D codes provides some error correction to cope with codes that become obliterated, smudged, or have ice on them. With a linear code such as Code 128, you have to read all the bars.”
“On the other hand, distortion can be an issue when reading 2D codes on curved surfaces, such as tubes. Scanners ideally want a flat surface, so a 1D code is placed running down the tube. Those codes are ideal for a round object and the smaller the tube, the more of an issue this becomes, since a lot of the label information is around the side and back. So a 1D code works really well when dealing with a small diameter, for example 8 mm. The problem is that the small tubes can be as short as 10 mm, which only leaves space for about four characters in a linear code. If you move to a 2D code then you might get 10–12 characters or even more, but the small tube diameter means that the code is wrapped around the side. So there are challenges on the small scale. Small 2D barcodes are also useful for bottom labels that can be read very quickly with a bottom-side reader. Once you get to larger tubes, like a Vacutainer™ vial containing a blood sample then 1D codes work really well because using Code 128 you have space for 12–16 numbers, or alphanumeric combinations.”
Is there a lot of flexibility in label size?
“Labels can be customized to any shape or size the customer wants, but are typically rectangular. One standard, Auto12-A, is being pushed in clinical labs and defines the size of the label itself – 1” x 2”, the 2” going down the length of the tube and 1” wrapped around it. This leaves a visible window on part of the tube to view the sample and the label is still large enough to hold a lot of either barcode or human-readable data.
What sort of conditions can labels withstand?
“Labels and adhesives can cope with a wide variety of conditions, including solvents like ethanol, methanol, DMSO, and xylene, and vapor-phase liquid nitrogen (-196 °C). We have some customers who over-laminate the text so that there is a clear portion of the label, a tail on the label that is wrapped around the printed portion to protect the printed part of the text from rubbing.”
What about re-labeling?
“One approach in the future would be read the label on a pre-labeled tube and, then make a new label that can be applied directly over the old one. OCR-based systems will be able to read the existing information on the tube and either replace old information with new information or provide an additional reference barcode. These vision-based systems, as they develop, will be able to provide that functionality.”
How do you see the future developing in barcoding automation?
“Systems will become more intelligent and flexible. Developments in OCR and cameras will help us to validate the label in terms of alignment with text and the barcode itself. The system should also be able to detect if the wrong label has been used, or even choose the correct label depending on the tube size. Advances in auto-configuration will definitely be a benefit for users down the road.”
“More and more labs want to standardize labeling. It’s a little like the standards developed in manufacturing, where a lot of companies started by doing it their own way and then edged towards a standard position. I think the trend is toward standardization on what information is applied to a tube, what barcode symbology is used, and the placement of the label.”
Click the link below to download the CLSI document, “Laboratory Automation: Bar Codes for Specimen Container Identification; Approved Standard–Second Edition”
About the author
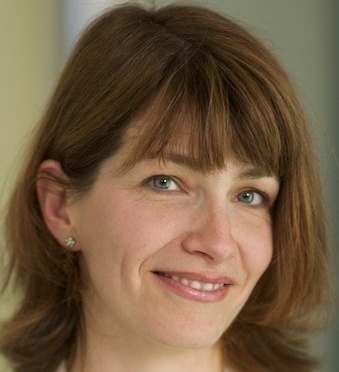
Florence Collins
Florence Collins is a product manager at Tecan Switzerland. She holds a master's degree in Agronomy. She joined Tecan Systems in 2000 as key account manager in California and moved to Tecan’s head office as product manager in 2006.