By Markus Vogler
Similar to the highly competitive automobile industry, clinical laboratories and manufacturers servicing the clinical diagnostics and life science markets, are always under pressure to increase quality and reliability. Likewise, they must at the same time cut costs and bring new products to market in a climate of rapid global change and increasing regulatory pressures. Specialist car manufacturers are leading the way with innovative new approaches to cope with the challenges. Those who are successful have learned how to be more adaptable and how to get their innovative products to market faster.
Can life science manufacturing apply some of the winning techniques of the automobile industry? We took a closer look at recent successes to find out.
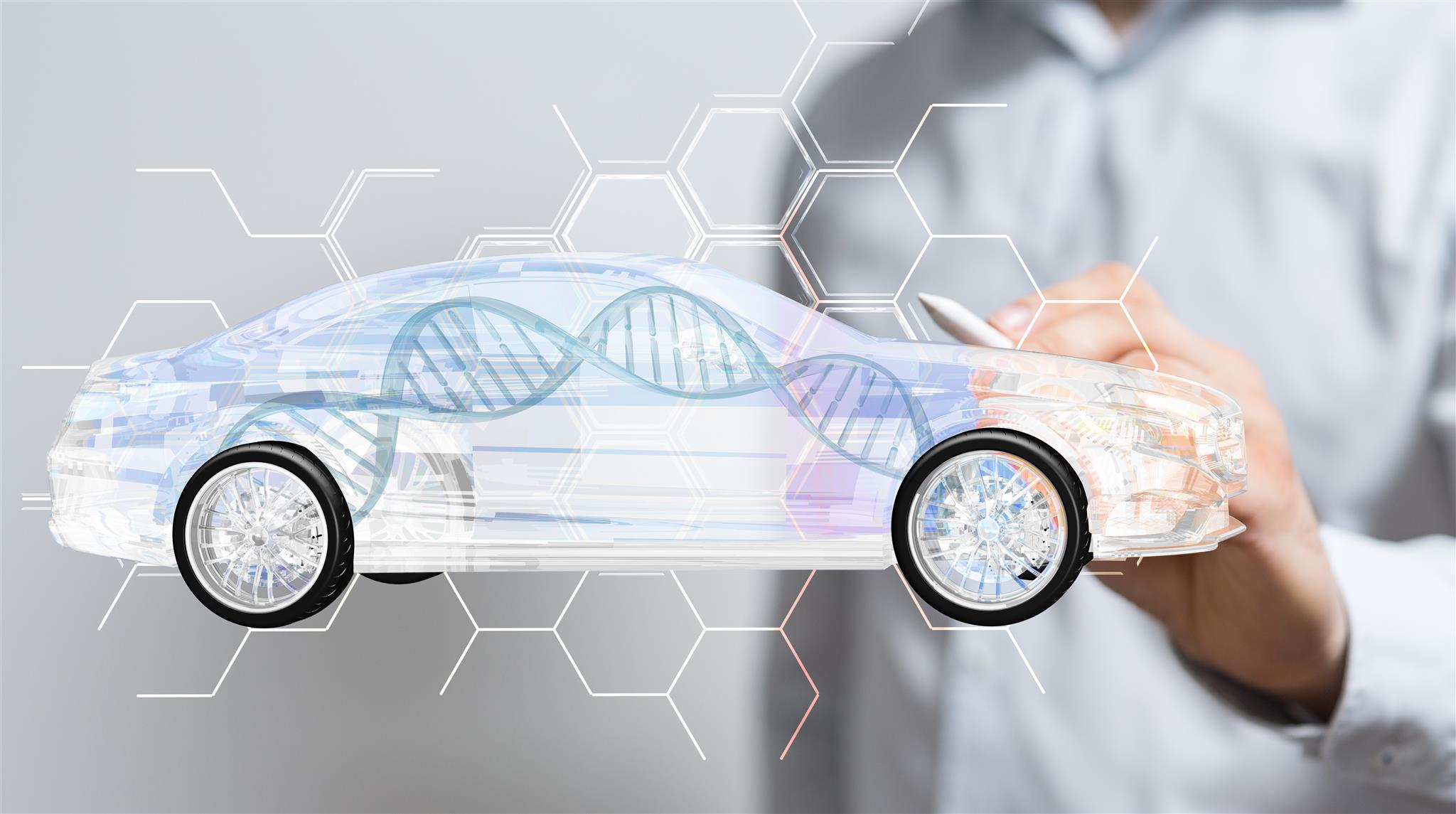
Here are six key insights:
1. Cutting edge robotics solutions give a competitive advantage
Leading car manufacturers are increasingly relying on robotics not just to increase efficiency but also to free up staff to focus on more creative and value adding activities. For example, German car manufacturer BMW is introducing lightweight movable robots, smart devices and exoskeletons to support workers and make the production system leaner and more adaptable.¹
Likewise, the clinical diagnostics and in vitro diagnostic (IVD) markets can take advantage of the latest in automation and robotics—for example, using advanced liquid handling robotics solutions instead of carrying out individual pipetting tasks or other types of manual handling. Tools such as intuitive interfaces, 3D simulation and reconfigurable systems allow product manufacturers to be more adaptable and to accelerate the development of new solutions for different market needs.
2. Reducing your footprint can significantly cut costs
In its new Kentucky factory, Toyota has exchanged the previous web of conveyor belts for moving pedestals that are guided across the factory floor by electronic sensors in the floor. In this way, Toyota has been able to downsize the plant from three to one story, thereby cutting costs considerably with regards to real estate, construction, heating/cooling, and maintenance.²
Reducing instrument footprint is just as essential for clinical laboratories. Smart robotics with compact dimensions can optimize use of space. New automation solutions can accommodate multiple devices and functions without expanding the instrument footprint, for example by using multiple levels for integration of devices into the deck space. This allows to expand the covered workflow section on particular instruments by reducing the total footprint and manual interfaces compared to multi-device solutions.
3. Productivity suffers when humans take on repetitive tasks
Many industries face the same challenges in their manufacturing – to eliminate human error, increase productivity, increase quality, conform to regulatory and quality standards and to free up staff for tasks where human cognitive skills are essential. At BMW, the lightweight robots mentioned in the first example perform tasks that are physically strenuous, repetitive and that demand a high level of precision. This means that staff can use their creative and cognitive skills to focus on value adding activities and quality management.
Similarly, companies within the life science and diagnostics markets are finding that machines trump humans when it comes to performing repetitive, boring and error-prone tasks. For example, solutions such as automated liquid handling systems and tools to automate laboratory research. Smart automation solutions can even integrate complex workflows on the same platform, thereby eliminating bottlenecks and errors, and increasing throughput dramatically.
4. The time to embrace individuality is now
For the automobile and clinical diagnostics industries – as well as for any other industry today – the increased individuality of customer demands adds external pressure. There is a constant need to cut costs, while customers at the same time demand unique and individualized products. The solution to the conflict between external variance and the need for internal standardization is modular platforms, which allow customization from standardized elements. Using modular automation solutions, manufacturers can make the equipment fit their workflows rather than making the workflow fit with existing equipment. As an example, the Volkswagen MQB platform is a modular solution that can be used for the construction of a wide range of cars, from the supermini class to SUVs.³
The clinical diagnostics industry can benefit from modular platforms by increasing internal standardization while still meeting the demand for acceleration of the market need for complex and individualized products. For example, modular OEM liquid handling components can dramatically shorten development cycles, secure investments by leveraging developments and thereby reduce time to market for manufacturers.
5. Hardware and software modularity makes it easier to adapt quickly
By introducing modular platforms, manufacturers can become more adaptable and be able to customize and offer new models at short notice. Modularity also allows for continuous improvements and for staying ahead of competition. With regards to Volkswagen, the MQB platform is more than a platform – it is a whole system for manufacturing different models at the same plant. In a way, modularity can be seen as a new mindset, a new way of looking at manufacturing and future manufacturing possibilities.
The best solutions include not only modular hardware but also modular software, where parts and software code can be re-used to create new configurations – without having to start from scratch. Software can be configured for a wide range of applications, such as molecular diagnostics, immunohematology, drug discovery or ELISA applications. Because, whatever the future will look like, manufacturers will not make the same things tomorrow that they are making today.
6. Built-in error-proofing is key to risk reduction
The automobile industry is using automation and data analysis to constantly improve its processes, not least when it comes to error-proofing. For example, BMW is using real-time analysis to control the status of parts, vehicles and machines. An automated system responds immediately should there be any damage or disruption. For example, if a delivery truck is involved in an accident, the system will calculate alternative routes and initiate corresponding measures for the workers.⁴
Similarly, for clinical diagnostics, smart software can allow for automatic quality checks. For example, software can be devised to simulate or predict which commands or keystrokes should be entered to initiate a particular workflow and use this information to check whether operators have followed the correct procedure. Using modular software, bits of code can also be re-used without changing the look and feel of the interface. This means operators will be more familiar with the software and less training will be required on new configurations, which in turn will further reduce the risk of errors.
Get more insights
Talk to a Tecan Expert about partnering and automation options.
References
1. Allinson, Mark, 2017 March 4, Robotics & Automaton News, BMW shows off its smart factory technologies at its plants worldwide.
2. Rothfeder, Jeff, 2017 September 5, Fast Company, At Toyota, The Automation Is Human-Powered.
3. Volkswagen Group MQB platform
4. Jukna, Lena, 2017 October 12, Living Map, BMW and the Smart Revolution in German Manufacturing.
About the author
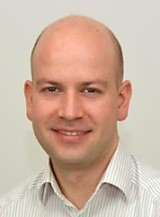
Markus Vogler
Markus Vogler is a portfolio manager at Tecan, Switzerland. He manages the modular technology and product portfolio within the partnering business division. His key focus lies around agile development, lean startup of new business models and innovation. Markus hold an MSc in Business development from Berner University of Applied Sciences. Markus joined Tecan in 2016 following the acquisition of Sias AG by Tecan.