By Kevin Moore
The trend towards more automated workflows in research is helping to significantly improve data quality as well as laboratory productivity. But when it comes to choosing an automated system for liquid handling and dispensing, it can be difficult to decide between the large range of technologies and platforms currently available. Here are a few pointers to help you select the features that are most important for your lab.
Automating your research? Don’t make the decision any harder than it needs to be.
Let the applications drive your choices
The typical research lab needs to support a wide range of current and future applications. For example, your lab might have a number of routine tasks like mycoplasma tests, ELISAs or BCA assays that are performed on a regular basis, while at the same time you might also be running more complex, multi-step processes like NGS sample and library preparation or cell-based screens. In many cases, there are “ready-to-go” automation solutions specifically designed to automate just one or a few types of applications.
While such solutions can offer a quick and economical way to get a particular procedure up and running, the downside is usually lack of flexibility. In the long run, purchasing several of these “closed” solutions to cover all your applications is not very cost efficient. It can also lock you into certain protocols and types of consumables. For example, it may not be compatible with a new type of tip that comes onto the market; or it may accommodate 96-well plates, but not 384; or it comes with a software program that you can’t modify to match a new protocol.
So, if like most labs, your application needs are diverse, ever changing, and sometimes more than a little complex, then a more “open” automation system may be the better way to go.
Flexibility will serve you well
The question is, what features and capabilities are going to give you the flexibility you need to handle many applications effortlessly? These 4 considerations can make a big difference:
1. Worktable capacity. At the top of my list is having a high-capacity worktable. Just as the amount of bench space in your lab dictates how many different tasks you can reasonably manage, the capacity of the worktable on your automated liquid handling system is a critical factor for productivity. To future-proof your lab, it makes sense to invest in a system with a large deck to facilitate high-throughput processes and full automation of multi-step workflows. The worktable should also be easy to reconfigure as needed to support a wide range of protocols and applications.
2. Modularity. Another big enabler is modularity, and with it the ability to integrate multiple peripheral components, so that you can start with the basics, and then add new functionalities as needs evolve and your budget allows. For example, Tecan offers a range of peripheral components that integrate seamlessly with its new Fluent® Gx systems. These include independently controlled incubators with heating and shaking capability, units for magnetic and vacuum separation, multi-mode readers and washers.
3. Integration capability. In addition to being able to integrate within the manufacturer’s products, your system should have options for integration with third-party platforms. For example, FluentControl supports straightforward integration of third-party devices, with an ever-increasing library of drivers – including support of SiLA devices.
4. Easy protocol transfer. For maximum flexibility and efficiency, it is also a good idea to check whether methods can be easily transferred between platforms by exporting and importing scripts, without time-consuming set-up of individual instruments.
Liquid handling and consumables support
An equally important set of considerations relates to the liquid handling technology itself:
1. Dispensing technology. This can be one of the most critical choices when it comes to getting robust and reproducible results. If you are likely to be working with solutions that vary a lot in viscosity and surface tension, then it’s important to think about whether you go for liquid or air displacement solutions. Worried about being locked into one or the other? Then consider a system that will allow you to easily switch between the two. Also, don’t forget to ask vendors about dead volumes, which obviously should be kept to a minimum to avoid wasting precious reagents and samples.
2. Volume range. The volumes you need to dispense can vary considerably across different applications. To avoid limiting your options, look for a system that accurately delivers a broad range of volumes, from sub-microliter up to milliliters. To some extent, the range may be determined by which dispensing technology you choose, and whether the tips are fixed or disposable.
3. Consumables support. The option of using disposable tips may be essential for certain applications—for example those with a high risk of cross-contamination, such as PCR and genomic library preparation. Accommodating different plate formats is another common challenge. To do so, you may need the ability to switch from fixed to disposable tips, or from 96- to 384-channel dispensing. You may also need appropriate robotic grippers to move tubes and plates to and from the readers, washers, incubators, magnets, vacuum units, balances or other modules integrated onto your workstation.
Delivering reproducible results
As we discussed in a previous article, (Crisis of confidence: How reproducible is your research?), the repeatability of biomedical research has become a major issue, and automating liquid handling is a given step in removing key sources of error. In my opinion, there is simply no room for compromise when it comes to system performance. The optimal automation solution should deliver consistent, reproducible and reliable operation based on high-precision and repeatable liquid dispensing.
Then there are the less obvious contributors to reproducibility. For example, mechanisms for automated sample tracking will help prevent mix-ups. Software that is easy to use will decrease the chances of operator error. The integrity and reproducibility of certain applications may also depend on having a controlled contamination-free environment, in which case the option to integrate a suitable laminar flow HEPA hood will be important.
In short, a good automation vendor should be sensitive to all of these needs, and be able to support any related claims. They should care as much about your research as you do!
Compliance readiness
Your work may well involve the rigors of regulatory compliance. If that’s the case, be sure to look for an automation solution that has been specifically designed to meet the needs of regulated laboratories, with all the advanced process security features required for applications in clinical, GMP and QC facilities that need to comply with stringent regulatory requirements, including FDA 21 CFR Part 11.
You will need to prove your system was – and continues to be – used in a compliant fashion, including audit trails and proof that no external changes to the system or record have occurred. Sample tracking should link sample IDs with results, and it should be possible to block unauthorized changes. The automation solution you choose should make these things as easy as possible for you.
Get support to make the right choice for your needs
Whatever your application, automated liquid handling can boost the reproducibility of your results and speed up your workflows. Tecan’s new Fluent Gx liquid handling workstations are built with the needs of research labs in mind, to help you generate reproducible data and automate your applications with flexibility that avoids constraining your lab work to a set pattern.
For researchers working in regulated environments, our compliance-ready solutions include assurance software that will make audits even easier. If your work demands fast and precise processing, high on-deck workload capacities, and intuitive operation, then Fluent Gx may be just what you’re looking for.
To find out more, talk to an expert now.
About the author
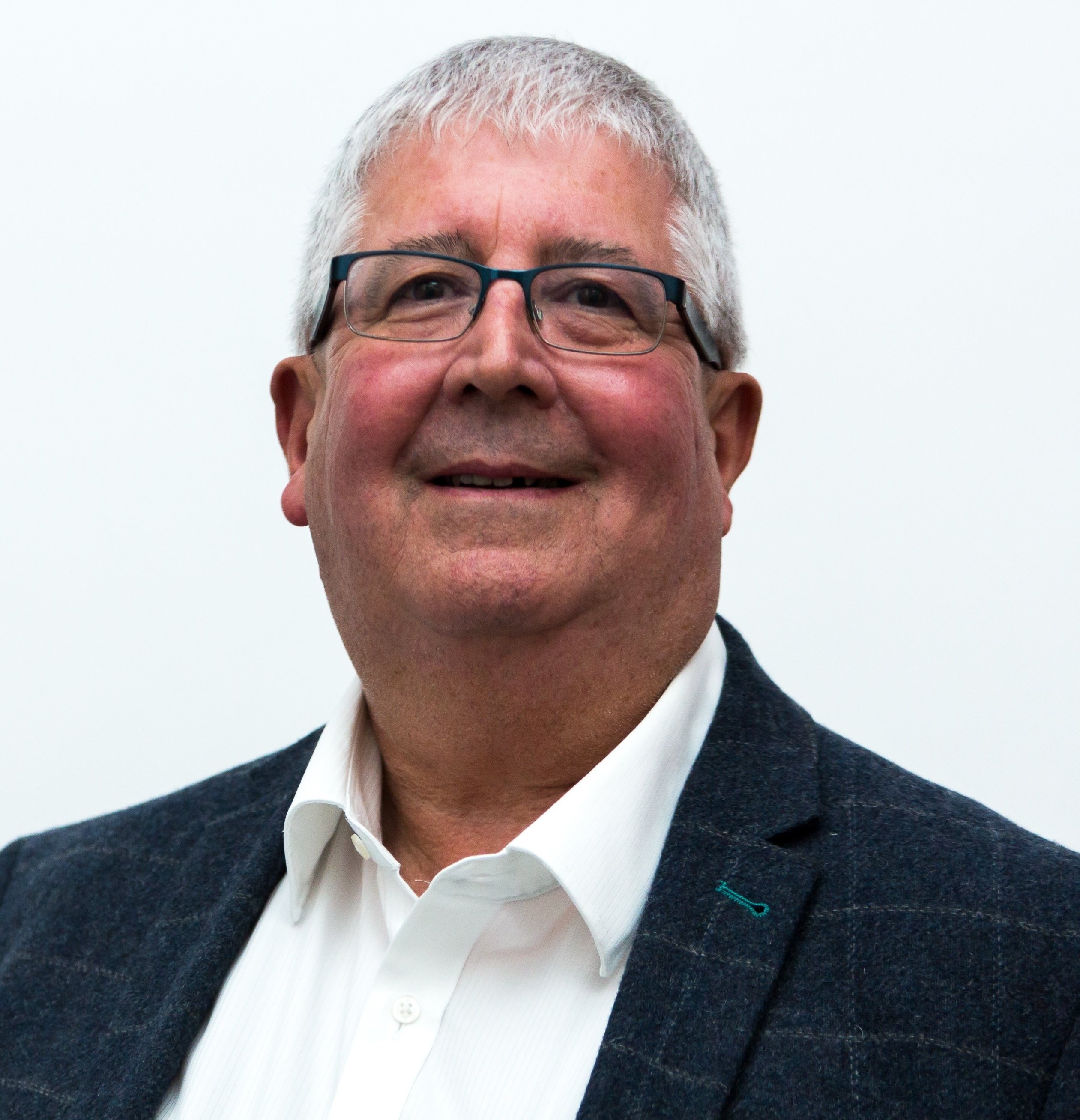
Kevin Moore
Kevin Moore is Head of Markets and Applications based out of Tecan’s head office in Männedorf, Switzerland. He heads the team tasked with bringing both products and application for the liquid handling to the market. Prior to joining Tecan in 2007, he was head of Compound Management and Technology project manager for the Neuroscience Research Centre of Merck & Co in the UK, where he worked for Merck for 20 years.