By Nicholas Smith
With open source software and high quality off-the-shelf components, do-it-yourself (DIY) lab automation solutions are trending. While developing lab automation in-house might seem attractive at first glance, the road is littered with hidden pitfalls that can derail internal projects. Finding an Original Equipment Manufacturing (OEM) partner can be a cost-effective way to circumvent the pitfalls and mitigate risks by working with a trusted automation expert.
DIY lab automation projects can cost more than you bargained for but an OEM partner can reduce the cost.
Lab automation is advancing fast, it’s time to get onboard
As lab automation becomes increasingly sophisticated, technology advances are making the dreams of increased lab productivity and throughput a reality, while simultaneously improving quality and compliance.
Often it seems logical to develop your automation solution in-house. After all, your company has the expertise, and outsourcing seems expensive. But do DIY systems really deliver? Before taking a do-it-yourself approach, it’s worth considering a few key factors that can significantly alter the cost and complexity of your lab automation project.
Handling the necessary trial and error
One of the first hurdles for an in-house project is the iterative nature of automated equipment manufacture, which usually involves a lot of trial and error. This can make accurate forecasting very difficult and increase the risk of going over time and over budget.
OEM partners not only have a lot of experience that can help you minimize trial and error, but they also typically use “agile” methodology to develop the equipment. Using agile means that workable solutions are produced as quickly as possible and then improved over rapid and successive production “sprints”. This approach makes the process very cost-efficient. Moreover, there is no nail-biting wait until the end of the project to see whether the machinery actually works. If there is a problem, the project team will find out early, so that it can be corrected as soon as possible. Any time saved can be used instead to focus on the finer details and improvements that will delight your end user.
A holistic view of lab automation is essential
When designing a lab automation project, it is easy to inadvertently cast your focus on certain key steps and forget to address some of the more holistic aspects that are equally critical to the success of your project. For example, developing a working prototype usually occupies most of the project resources, but will this be at the expense of software development and lifecycle management?
OEM partners have experience in managing all elements of lab automation. Not only do you get the lab automation system, but you also get the tried and tested software complete with error logging and updates. With an OEM partner, you’ll also get lifecycle management built in so that you know exactly how long the automation system will last, as well as how and when it should be upgraded. Without adequate lifecycle management, unforeseen upgrade costs can crop up in the future, jeopardizing the sustainability of your product.
Keep the regulators and auditors happy
If you are developing automated solutions for use in medical diagnostics or other highly regulated industries, your system design and lifecycle management plans will need to take into account an increasingly stringent regulatory landscape. Even if your automation products are not intended for use in such contexts, automation of almost any manufacturing process has associated safety and quality standards that you will need to satisfy. So regardless of the application, you will almost certainly need to be able to generate relevant paperwork to get your equipment approved and to pass any related audits.
Instead of placing this burden on your internal team, who may not have much regulatory expertise, you can outsource the work to your OEM partner. They should be able to provide examples of where they have dealt with regulatory bodies such as the FDA and advise you what paperwork they can provide to make approval and auditing as simple as possible.
Make sure there are no essential skills missing
It is easy to think you have enough skills internally to successfully complete a DIY lab automation project, but after deeper research many organizations find that this is not the case. Maybe you have a top-notch engineering team, but are they equally skilled in software development? Do you also have a regulatory expert on hand? If so, will that person have the time and depth of experience needed to make sure everything is up to standard? Do you have project managers who can give oversight on the lifecycle of the project to make sure that you always have a cost-efficient automation solution in your product arsenal? Without these, a DIY automation project may turn out to be short-lived and extremely costly.
For OEM partners, lab automation is their core business, so they should automatically have all of the technical skills required to complement your industry knowledge and deliver your lab automation vision.
How long will an in-house project really take compared to an OEM partner?
All these potential pitfalls put enormous pressure on the project timeline, which often ends up being stretched in order to accommodate delays. This is coupled to ballooning costs and knock-on effects in other projects when resources are tied up for longer than expected.
Working with an OEM partner means that there are far fewer opportunities for the timeline to overshoot. Assuming requirements have not changed, you have an experienced partner to help you make up the time. By tapping into all the added possibilities that an OEM partner brings to the table, you can deploy internal resources more strategically and improve your productivity as a whole.
Take advantage of flexible financing from an OEM partner
The mounting hidden costs in DIY solutions make OEM partners a very cost-effective option for any business wanting a low risk, high quality lab automation product. An OEM partner may be able to offer you more flexible financing options than you could otherwise manage. And that means that outsourcing may well be within your reach, even if you are on a tight budget.
Lab automation projects require a diverse array of expertise that extends beyond just the core hardware. If any of these skills are missing, then your project can quickly become derailed. Working with an OEM partner is a way to guarantee the quality of your product and avoid the disappointment of a project being cancelled due to runaway costs or unexpected regulatory hurdles.
Are you ready for your next lab automation project? Get a free copy of our self-assessment checklist here.
About the author
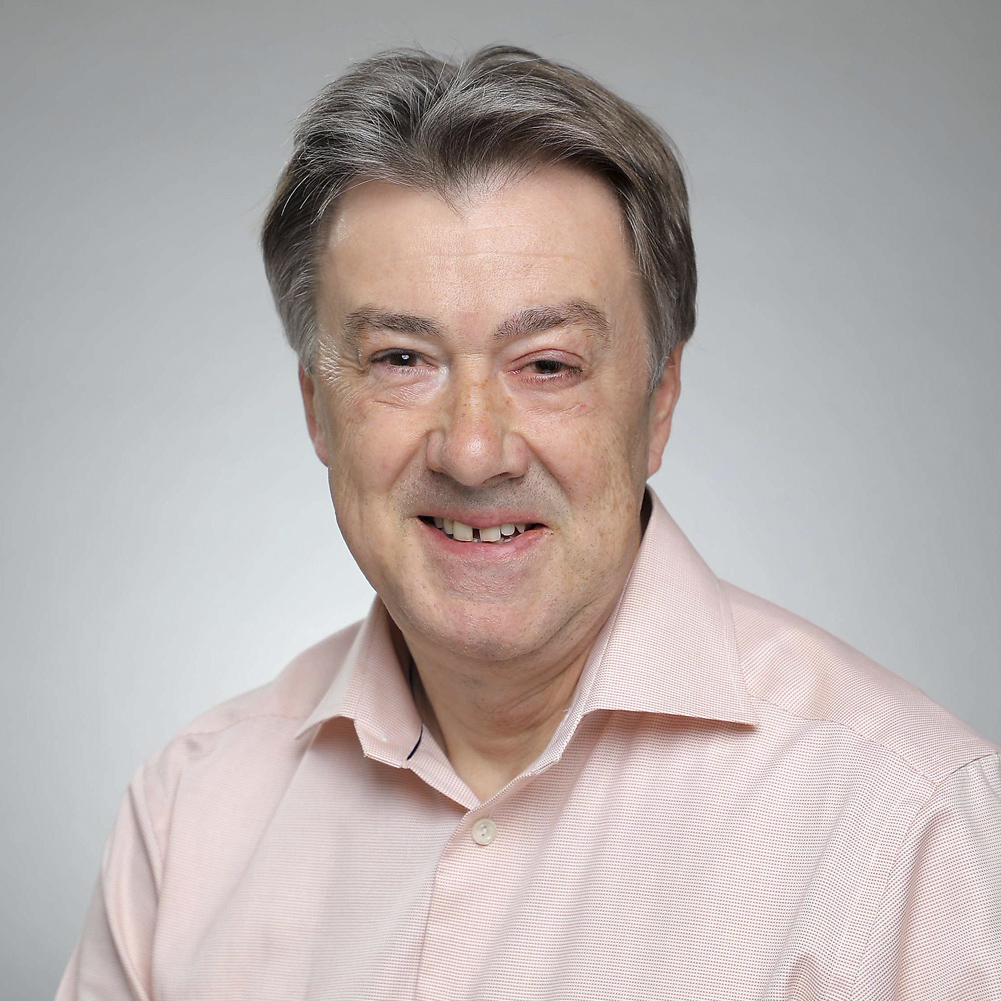
Nicholas Smith
Nicholas Smith is Head of Global Marketing and Portfolio Management for Tecan’s Partnering Business. A key function of his team is to work closely with customers to develop new product concepts and proposals based on a thorough analysis of their specific requirements. Nicholas’ joined Tecan in 2012 from Roche Diagnostics where he worked for over 20 years in a variety of roles within marketing and business development.