By Claudio Bui
The demand for advanced medical and diagnostic testing continues to accelerate. Laboratories, hospitals, and emerging consumer genomics companies are demanding quicker test sequences resulting in the design and development of new innovative and responsive test protocols. These new tests include the handling of a wide array of fluids. The measurement, monitoring, mixing, and controlling of solvents, salts, detergents, acids, bases, reagents, and additives is critical in all liquid handling lab environments.
These liquids are pumped, dispensed, and aspirated both manually and automatically. They come in contact with pumps, valves, manifolds, and syringes made of any number of materials — PTFE, PCTFE, PEEK, PPS, UHMWPE, FFKM, stainless steel, and glass, just to name a few. With so many possible combinations of chemicals and component materials, how can you be sure that the components you choose for your automated liquid handling system are the best choices for the chemicals to be used in testing?
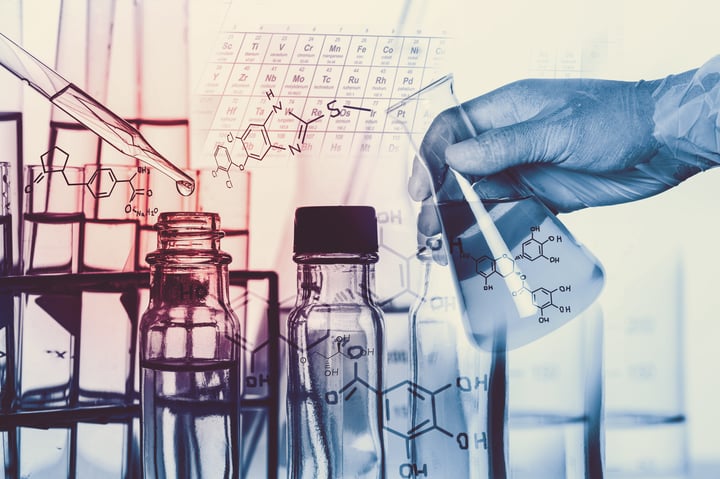
By carefully matching the compatibility of your liquid handling pump material with the chemicals that will be used, you can help to ensure the reliability, functionality, and long-term performance of your lab automation instruments.
Beyond the chemical compatibility chart
Following are six considerations that will help you avoid unforeseen and costly design failures, reduce development time, and speed up time to market, while ensuring that your automated liquid handling system performs as expected for its designated application.
1. Identify the material that meets your needs. Even chemicals with the same name may not be equal.
Chemicals used in biotech and pharmaceutical workflows may vary greatly – even for a single application. It is essential to consider the exact formulation and chemical concentration to be used in testing in order to select the correct pump material for your instrument. Even the slightest variation could result in catastrophic performance failure. For example, sodium hydroxide (20%) may be well contained in a manifold made of polycarbonate. However, that same chemical at 80% concentration running through that polycarbonate manifold may have severe effects, including shortened life span and possibly leakage. A better alternative for the manifold material with this chemical concentration may be PEEK.
Keep in mind that chemical compatibility is rarely a binary condition. Biotechnology and pharmaceutical applications almost always involve more than one chemical and varying experimental conditions, any of which may affect compatibility and material reaction. Make sure to identify and assess all factors that may influence your choice of materials for your specific liquid handling components.
2. Use a chemical compatibility guide
Take advantage of the easily accessible chemical compatibility charts – a quick online search will yield reliable and valuable guidelines. Most laboratory and industrial fluid providers offer temperature and compatibility data on the chemicals they supply. One such compatibility guide is the Cole-Parmer Chemical Compatibility Database.
Most online chemical compatibility charts are just rough guides. They provide a rating based on available information and on how the named chemical will or will not degrade any materials encountered in the fluid path. Chemical resistance ratings may be based on a scale ranging from A to D, or Excellent – no chemical interaction, to Severe – resulting in failure of the material to properly contain the chemical. Imagine the outcome if the pump materials in your liquid handling device fails: your customers may experience tainted test results, testing down-time, and possible instrument redesign.
3. Consider how operating conditions might impact chemical compatibility
The compatibility of most detergents with stainless steel 316 (SS 316) is rated Excellent. However, compatibility with some reagents begins to diminish above 22ºC, which is just about standard room temperature. It is well below human body temperature (37ºC), which is used as a sustaining temperature in many experiments done with live cells. So if the operating temperature in the test application will be above room temperature, you might consider ceramic components. Ceramics are rated Excellent in compatibility with detergents and have no significant constraints for common biochemical or pharmaceutical workflows.
4. Confirm the exact materials for your components
The solid materials that liquid handling components are made of can also come in different formulations. SS 304 and SS 316 are often adjacent on the compatibility charts. Does the difference matter for life science applications? It does. A wide range of salts are used in pH buffering solutions for biochemical applications. The compatibility of the commonly used salts with SS 316 is rated Excellent, whereas the compatibility of SS 304 with salts has a slightly lower rating of Good. Why the difference? It turns out that SS 316 is formulated with a tiny bit (2%) of molybdenum specifically to increase resistance to salt. A component made of SS 304 might be unsuitable for use with common biochemical buffers. When consulting the chemical compatibility chart, be sure that you assess the exact pump, valve and manifold material available for your components.
5. Choose the material that offers the lesser of all evils
Of course, the requirements for the fluid path are not the only consideration in choosing your components. There are many other design requirements that dictate features of your pumps, valves, and manifolds. And there may be no perfect choice.
When faced with this dilemma, it is helpful to consider what types of deleterious effects your instrument can tolerate. For example, the impact of bleach on polyetheretherketone (PEEK) is severe pitting and corrosion, even at low concentrations. Such extreme corrosion in a pump, valve, or manifold will quickly degrade the performance of a precision automated liquid handling system to an intolerable condition. In contrast, a less severe and more tolerable chemical and component pairing may only result in discoloration.
6. Be confident that your pump material has been selected correctly the first time
When incompatible materials come together, at least one of them and possibly all will suffer. If degradation of the component materials results in near-term failure, you will not only lose time but also money. If your instrument is released to the market, the impact on your customers will be even more detrimental. They may experience premature failures, reduced life span, poor performance in the form of false results, failed runs, and wasted samples, not to mention the damage that failure may cause to your brand name.
Careful selection of the right materials for your pumps, valves, and manifolds will ensure your lab automation system is designed right the first time, performs as required through application testing, and can be released to the market with assured quality and reliability. More importantly, when your customer uses your product they are more likely to attain the results they expect and move their work forward more quickly and efficiently.
Fortunately, components for liquid handling automation systems are available in a variety of materials to ensure compatibility with all of the chemicals commonly used in biotech and pharmaceutical applications. If you have questions about the chemical compatibility requirements for the pump, valve, or manifold in your liquid handling instrument, talk to Tecan.
Want to know more about liquid handling components?
About the author
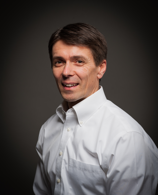
Claudio Bui
Claudio Bui is the Head of Product Concepts for the Partnering Business in the Components Marketing Team. The primary function of his team is to work closely with customers to develop new concepts and proposals based on a thorough analysis of their specific requirements. Claudio started at Tecan in 1990 in R&D developing Components and has been involved in the development of a number of small laboratory instruments. In 2005, he joined the Marketing team.