By Claudio Bui
When you design a complex laboratory automation system or device, every OEM liquid handling component that you integrate into it should be reliable, dependable and expected to perform to the highest industry standards. Subpar quality is not an option. If the intended use of the system includes critical tests for clinical diagnostic purposes, the consequences of failure or poor performance of liquid handling components could be more costly than you bargained for, including irreparable damage to your company’s reputation and even worse – it could pose serious risks to patients’ health. Integrating components into your system that are reliable and have a durable design should be an essential consideration.
Ensuring reliable long-term performance of your OEM components goes beyond regulatory compliance and published performance specifications: it’s also about the right pre-validation and pre-testing. What should you look for?
How can you ensure that your OEM parts and liquid handling components will perform reliably throughout their entire life cycle?
As engineers, we know that there are no absolutes, and there are many factors that can affect system performance. What is within our control is the ability to mitigate the risk of having a product fail prematurely by selecting components that are robust and reliable and provide a generous safety margin. Ultimately, the reliability of the system design is determined by the weakest component in the system. For that reason, thorough OEM supplier qualification is a key first step to mitigating the risks.
Here are some practical considerations that should be at the top of your list when choosing a liquid handling components supplier or OEM partner:
- Select components from a supplier that has a proven track record, a history of quality, and a clear focus on reliability.
- Partner with a company that takes quality seriously - a company that understands the importance of meeting the highest standards of quality control, reliability, and regulatory compliance.
- Look for a company that operates under a quality system that complies with ISO 9001 and ISO13485 standards.
- Are social and environmental considerations important to you? A company that takes the health of the world they live in seriously will also take your concerns seriously. Look for a company that complies with RoHS, REACH and WEEE.
- Purchase from a company that offers you UL-recognized components to help you streamline your end product’s UL certification process.
- Consider the importance of life-cycle testing; liquid handling components that have been thoroughly tested at the factory to ensure that they meet your quality requirements will safeguard the long life of your system.
Top three reliability indicators for OEM pumps and components
Comparing pumps or other critical system components on the basis of product specification sheets alone can be a mind-boggling task. The impact of seemingly minor differences in specifications may not be apparent until months or years after installation and performance. By this time the damage is done, tests may have been compromised, and the samples consumed by poor quality and unreliable components. Your reputation, your company’s reputation, and your customer’s reputation may all have suffered.
In addition to working up a good supplier qualification checklist, consider these three reliability indicators when determining whether your liquid handling components are reliable and will perform over the long-term:
1. Regulatory compliance
Some applications require that your OEM components meet regulatory requirements such as ISO 13485. Even if you aren’t building equipment for medical use or other highly regulated applications, consider the added value that fully audited verification of regulatory compliance brings to ensuring the reliability of your OEM liquid handling pumps.
Regulatory compliance verification is more than just a stamp of approval on medical devices. It is an indicator that the manufacturer upholds the most stringent quality standards. Compliance verification requires rigorous testing against design specifications, as well as ongoing monitoring, maintenance, control, and documentation of all participants, processes, protocols, and uses related to design and manufacture of the product. Verified providers are regularly audited and records must be maintained throughout the lifetime of the device.
Whether you need specific regulatory certifications or not, liquid handling pumps that are certified must be designed, built, and tested to demonstrate that they meet international quality standards for robust and consistent performance.
2. Testing transparency
The performance of your liquid handling pump is critical. The volumetric accuracy and precision of your final system will depend on the accuracy and precision of the pump itself, and secondarily on the various other components present in the liquid path of the system. It is important to remember that each component in the liquid path contributes to or affects the overall system performance.
There are two tests primarily used for confirming volumetric accuracy and precision:
Gravimetric testing confirms the volume dispensed based on the weight of a fluid sample dispensed onto a calibrated balance. This is typically a system-level test that takes into account the presence of the syringe, the valve, tubing, and the probe.
Linearity testing uses a high-precision measurement device that tracks the mechanical movement of the syringe carriage to determine the dispensed volume. This is typically a component-level test.
In addition, there is a third test that may also be implemented:
Force testing applies a calibrated weight to the pump carriage to verify that it can lift the weight for a specified number of cycles. This ensures that the drive motor, drive mechanics, and electronics all function as expected to produce sufficient force for the required fluids and applications.
Any tests that are completed by your OEM partner prior to receiving the component will provide the added value of streamlining instrument testing on your end and ensuring long-term reliability.
An OEM provider that understands the value of accuracy and precision will calculate and store the results of all these tests with the device history record and refer to them as needed for development and troubleshooting.
3. Chemical compatibility
High concentrations of salts, solvents, acids, or bases can all lead to corrosion of the pump and other components in the fluid path. Material degradation can cause declining reliability of the pumps, possibly leading to unpredictable and inaccurate results. Of course, the first step in avoiding corrosion of liquid handling components is to choose pump materials that are compatible with the end-user’s fluids by considering the chemical compatibility requirements.
Even with the correct pump material, carefully-designed wash routines that incorporate appropriate wash solution(s), timing, and number of wash cycles may be critical to minimizing long-term exposure to corrosive materials within the fluid path. When creating a wash routine, consider the benefit of adding steps to keep pumps in motion in a safe wash solution while the pump is idle, thus protecting mated surfaces in valves and syringe plungers, particularly with salt-based buffers that may crystallize on surfaces.
Knowing how to protect your OEM pumps from long-term degradation before you buy can help you to design safe and effective wash protocols that will ensure reliable performance of your liquid-handling components.
You carefully test all of your sub-assemblies and final products before they go out the door. You shouldn’t have to test each component for long-term robustness as it comes in the door.
Talk to a Tecan expert to learn how Tecan pre-testing processes ensure that the pumps you buy will deliver the performance you require throughout their lifetime.
About the author
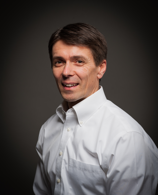
Claudio Bui
Claudio Bui is the Head of Product Concepts for the Partnering Business in the Components Marketing Team. The primary function of his team is to work closely with customers to develop new concepts and proposals based on a thorough analysis of their specific requirements. Claudio started at Tecan in 1990 in R&D developing Components and has been involved in the development of a number of small laboratory instruments. In 2005, he joined the Marketing team.