By Kevin Moore
Automated liquid handling can eliminate many tedious tasks, improve your productivity and free up valuable time for better things…but only if you implement the right solutions. Whether you are working in genomics, cell biology, drug discovery, molecular diagnostics or something completely different, the right liquid handling system can make your life a lot easier. We’ve collected some of the most important questions to consider before taking the plunge with a new automated liquid handling system.
Automating your liquid handling tasks can free up time for other pursuits.
1. Are you starting with a robust manual process?
Liquid handling automation can greatly improve a manual workflow, but it cannot fix an assay that does not already work manually.
Before trying to automate your process, make sure you have a successful, robust assay and that you fully understand how your process works. Breaking your workflow down into individual steps will help you select the elements you need for an efficient, integrated automation solution. Consider in advance how each step and the overall workflow might impact your process.
For example, taking an assay from a manually pipetted, tube-based format to an automated, higher density, plate-based workflow means that the samples and reagents will be on the deck for a much longer period of time. How might this affect the integrity of your samples and reagents? Details matter.
2. What level of walkaway automation do you need?
Walkaway automation describes the ability of a system to run without manual supervision or intervention. Minimizing human intervention by letting robots take over the tedious and repetitive tasks offers several important advantages:
- increased reliability
- cost reduction
- less chance of human error
- more time for you to focus on designing experiments, interpreting data, and other important tasks
Building in automated liquid handling carries an upfront cost, however, so it is wise to distinguish between what elements you consider essential and what it would be nice to have.
You can design your system for one level of walkaway automation now, with built-in flexibility to increase it in the future.
3. How will your needs change?
To save money, it might be tempting to automate only to meet your lab’s current needs, but in the longer term you could lose out. It’s well worth considering up front how your system might be used in the future.
A good automated liquid handling system should be reconfigurable, so that you can take on new applications and workflows as needs change. With a flexible, modular system, many elements of your current workflows can be repurposed and upgraded.
4. Is there an off-the-shelf solution to meet your needs?
Some smaller, specialized workstations have been optimized for specific applications with proven protocols, such as for DNA extraction, sample preparation, or cell culture. If a dedicated workstation meets your current needs, this could vastly simplify your selection process and still be a useful core component to integrate into a larger system in the future.
But take care to avoid “closed” inflexible solutions. It is definitely worth the extra effort to search for off-the-shelf solutions that have been designed with future integration and flexibility in mind.
5. How much lab and bench space do you have, and are you using it efficiently?
In today’s lab environment, space is a precious commodity. Most liquid handling systems are now multi-user, which has increased the demand for flexibility and innovative space design.
Consider the possibility of adding automation that can access space below the bench. Floor-standing liquid handlers can access the bench top as well as instruments or labware storage units below tabletop workstations, for example.
6. How easy is it to maintain and service?
Whatever solution you are considering, it pays not to overlook the issue of servicing and maintenance. Ease of access by technicians can reduce downtime and disruptions to your workflow.
7. Have you thought of everything?
Aside from productivity factors, there is much more to consider when choosing and setting up a new automated liquid handling solution, including:
- Which choices to make to minimize human error with liquid pipetting
- What to consider when integrating peripheral devices like plate readers
- The most important features and functions to look for in system software
To learn more, download our helpful guide now.
About the author
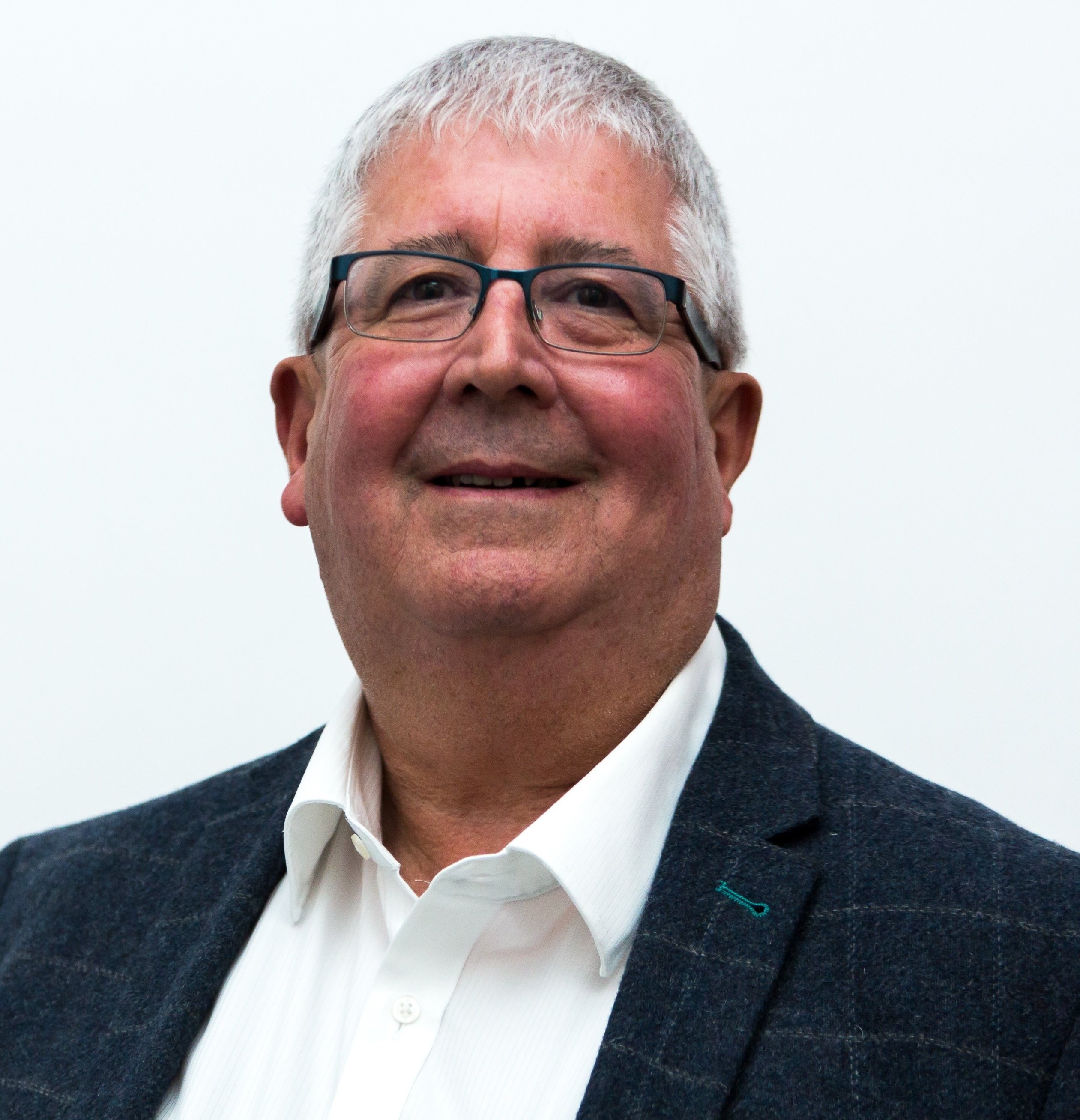
Kevin Moore
Kevin Moore is Head of Markets and Applications based out of Tecan’s head office in Männedorf, Switzerland. He heads the team tasked with bringing both products and application for the liquid handling to the market. Prior to joining Tecan in 2007, he was head of Compound Management and Technology project manager for the Neuroscience Research Centre of Merck & Co in the UK, where he worked for Merck for 20 years.