By David Wold
The impact of pump pressure sensors on your automated liquid handling pump performance is often underestimated and underappreciated. The saying, “You don't know what you’ve got ‘till it's gone” applies to many things in life – including fluidic pumps. When device sensors are doing their jobs, the end-user will never know, but when the sensor feature fails to perform, the consequences can be costly and catastrophic. Today’s smart technologies empower pressure sensor functionality more than ever. Why are pump pressure sensors essential for automated liquid handling systems? What benefits do they offer? How do they increase functionality and address process security risks?
Pump pressure sensors play critical roles in automated liquid handling for life science applications, and are empowering better process monitoring, error-handling and diagnostics.
Why are integrated pump pressure sensors critical for end-users?
Pump pressure sensors are essential for reliable system performance, as well as for enabling a wide range of functionalities. One of the primary functions of pressure sensors in liquid level detection (LLD) is to ensure accurate pipette submersion. Moreover, pump pressure sensors are used for leakage detection, preventing false positive LLD caused by bubbles or foam, and process security. These functions are critical to the uninterrupted workflow of any assay:
Ensuring precision and accuracy
Pump pressure sensors monitor the aspiration and dispensing of samples, reagents and liquids of any viscosity and surface tension. They play an integral role in minimizing and even avoiding tip contact with fluid, and help avoid foam, air bubbles and clogs. For instance, during genomic sequencing and diagnostic testing, pipetting errors, as a result of imprecise or inaccurate aspirating and dispensing, may result in inaccurate sample volumes. This can translate into failed sequencing runs, wasted samples, delayed results, costly misuse of reagents and potentially misdiagnosis.
Bubbles or foam in sample wells make liquid level detection difficult. Aspirating and dispensing within these obstacles may lead to pipetting errors and inaccurate volume displacement. Fortunately, pressure sensors and air displacement technology offer accurate and precise liquid handling in automated fluidic workstations.
Prevent leakage by maintaining your pump seals. In order to know what to watch for, it is important to know how your automated liquid handling pump syringes are constructed. There are likely to be stationary points of contact, for example where the syringe is secured to the valve port. Leaks here can lead to loss of valuable sample or inconsistent pressure. Seals between moving parts such as between the plunger and the barrel are also critical to minimize leakage and ensure accurate and precise dispensing.
Minimizing reagent consumption
Reagents are a precious commodity. Inaccurate fluidic measurement during the pipetting process may require the repeat of tests and experiments. This leads to unnecessary additional costs and time. In some cases the work may not be repeatable because of limited test samples, e.g. when processing rare DNA and patient samples. Minimizing contact between tip and sample conserves liquid and ensures that no additional liquid is wasted as a result of adhesion. Again, tests that have to be repeated due to inaccuracy will lead to wasteful, and costly reagent consumption.
Preventing cross-contamination
Cross-contamination is a potential error source and must be avoided. This is particularly important when processing clinical samples. Pressure sensors reduce cross-contamination in two ways:
- To limit tip submersion into the liquid sample: as a result, there is less chance of fluid collecting on the outside of the tip and mixing with another fluid.
- To detect leaks: this involves monitoring and reporting on leak decay in the fluidic path that may prevent proper fluid transfer.
Enabling self-diagnostics
Pressure sensing data may be used for self-diagnostics. Monitoring of pressure may indicate a degradation of your consumable parts, improper syringe installation, or tubing issues. Identifying these issues early may protect the pump and electronics from serious damage and maintain system uptime.
Overall process security
Process security technologies expose anomalies interfering with the liquid handling and data reporting functions. Pump pressure sensing provides process security throughout an entire test process. Detecting errors early and reliably allows the operator to make corrections and halt poor processes, saving time and precious fluids.
How do integrated pump pressure sensors add value to automated liquid handling workflows?
Prior to starting a run: Data from integrated pressure sensors may be used to monitor fluidic paths for proper workflow. For example, NGS library preparation kits used for genomic analysis can cost thousands of dollars. If a test run is set up improperly, the kit is wasted, and the library preparation needs to be repeated.
During a test run: Pressure sensing can be applied to monitor fluidic performance during aspirating and dispensing. The data are used:
- In LLD to minimize the submersion depth of tips. This avoid excess contact with sample fluids and reagents
- To maintain pressure in the tip and ensure that fluidic volume remains constant during robotic arm movement across the work deck
- To report inconsistencies during aspirating and dispensing to detect clogs, air bubbles, and missing fluid
At the end of a run: Log files provide process data that may enable analysis to determine whether a protocol is performing consistently run-to-run, distinguishing any abnormalities.
For pump diagnostic testing: Pressure leak decay tests ensure proper fluidic paths at all stages of the assay.
How are pump pressure sensors enabling smarter solutions?
Advancements in sensor technologies enable better processing capabilities and communication interfaces. Self-diagnostic testing will become more prevalent. Machine learning algorithms are emerging to analyze performance. Pressure sensors may provide a pivotal data stream for bringing machine learning into the life sciences robotics industry.
Pump pressure sensors and automated liquid handling – a perfect match
Including the right liquid handling pump in the instrument design will provide robust performance, improve time to market, and increase customer satisfaction. It is essential to look for pumps that incorporate high-quality sensors that are right for your intended applications and performance capabilities.
Do you want to learn more?
To find out about Tecan’s innovative Cavro pumps with integrated pressure sensor technologies contact one of our experts today.
About the author
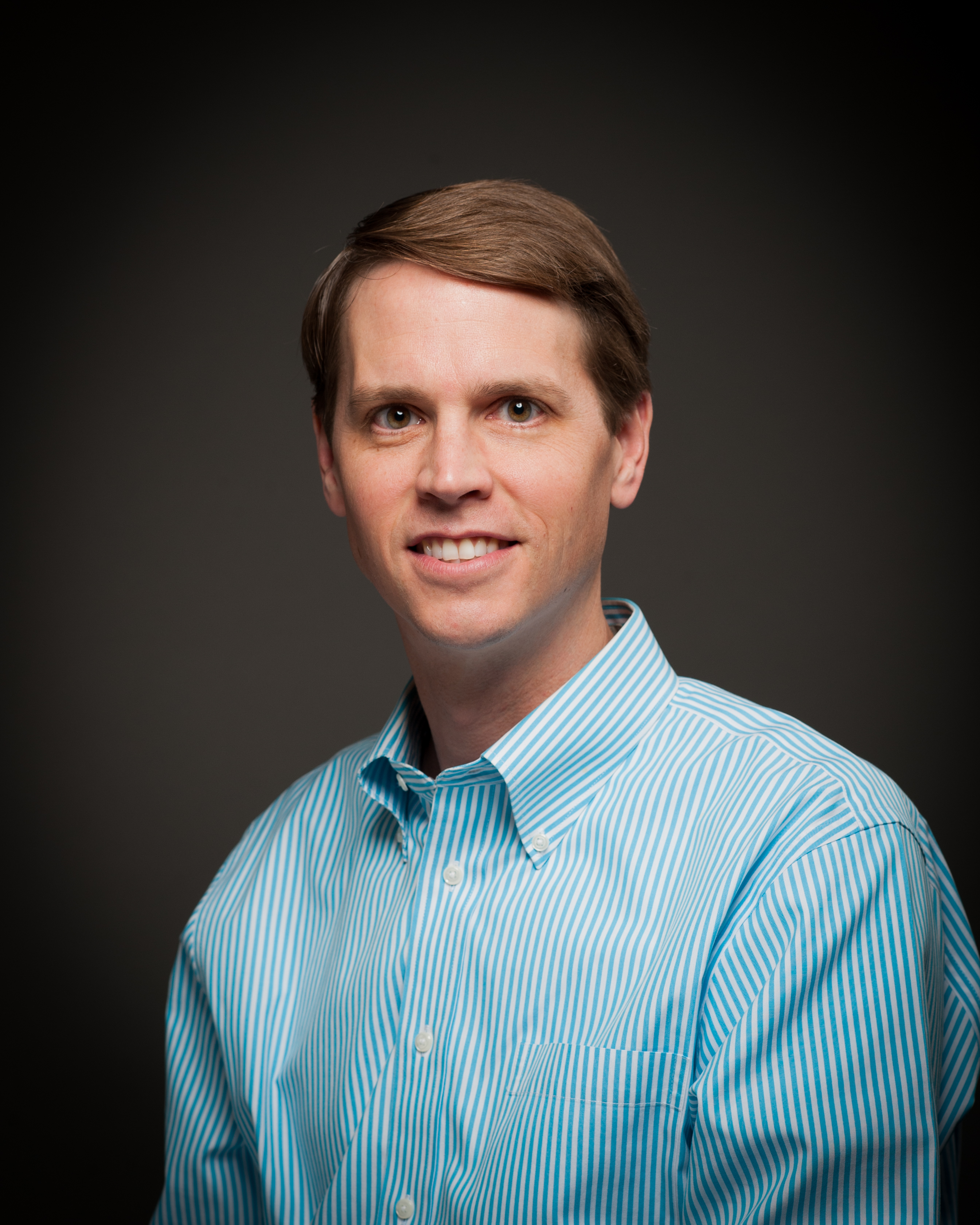
David Wold
David Wold is the Customer Operations Manager for the Partnering Business in the Components Marketing Team. In this role, he oversees a team responsible for the support and satisfaction of Tecan’s top Components customers. Since 2005, David has helped Tecan customers meet their liquid handling challenges across a broad range of technologies and applications. He brings understanding and expertise to help customer choose components to meet their needs, provide maximum reliability and outstanding performance.