By Michelle Aichele
As we move into the 2019 budget cycle with signs of a global economic slowdown on the horizon, laboratory administrators are no doubt feeling the heat. A combination of poor forecasting, inefficient use of resources, and a sudden economic downturn could create the perfect storm to capsize operations. Despite these high stakes, critical decisions about budget allocation, expensive equipment purchases, workflow optimization and cost-cutting strategies are often made based on incomplete information or even pure guesswork about laboratory asset utilization.
How much do you really know about how and when your instruments and consumables are being used? Could better use of existing data be the key to overcoming this recipe for disaster?
Increased visibility of instrument utilization data and better asset management could potentially save your lab valuable time and money.
In our uncertain economic climate, laboratory managers and administrators are constantly challenged to minimize risk and squeeze more out of their hard won budgets and resources, even at the best of times. “More, faster, better” is the universal imperative that finds its way into virtually everyone’s performance targets. Year-on-year it gets increasingly difficult to further streamline operations and come up with new strategies to drive cost-efficiency. Having an inaccurate picture of how laboratory equipment and consumables are used can result in missed opportunities and costly mistakes.
Laboratory asset management: the high cost of not knowing enough
A typical R&D lab may have 2 or 3 pieces of capital equipment per scientist, totaling upwards of $1 million USD or more. Larger organizations such as clinical reference laboratories, contract research organizations and pharmaceutical companies can be managing extensive fleets of high-end robotic systems deployed globally, bringing the total closer to $1 billion USD.
Given these large investments, and the critical nature of the work they support, it is sometimes surprising how little is understood about how equipment is being used in the laboratory. How many hours per day is each system actually running, and what is the burn rate for associated consumables, such as pipette tips and sterile tubes? How could scheduling and workflows be adjusted to increase lab productivity? Which robots are performing sub-optimally? When should they be replaced, retired or redeployed?
Accurate answers to questions like these are vital for optimizing productivity, coming up with effective cost-cutting strategies, and making sound capital investments. Without this information, it is virtually impossible for a lab to get the most out of equipment investments. Your lab could be wasting an inordinate amount of time and money without anyone even realizing it. For example, you might:
- Purchase instruments and equipment that are not really needed
- Incur excessive service costs from unplanned maintenance or by having the wrong type of service contract in place
- Experience a disruption of operations when equipment fails or requires an unplanned service visit
- Encounter bottlenecks and long turnaround times arising from inefficient use or deployment of equipment and resources
Instrument utilization data could be your lab’s biggest asset
So although it doesn’t typically appear on the balance sheet, instrument utilization data could be your lab’s most valuable asset. An analytics solution that enables you to visualize and analyze instrument and consumables usage in real-time could fill in the gaps needed to make more informed decisions. For example it could provide the missing piece of the puzzle needed to:
Increase efficiency and productivity – Historical instrument usage patterns may highlight capacity gaps, help you minimize downtime, and improve troubleshooting. For example, you might discover that instruments are underutilized at the beginning of every shift, or on a particular day of the week. Periods of over-use might be associated with higher failure rates, or indicate the need for an additional instrument or redeployment of existing equipment to ease the workload.
Enable more rapid responses – Real-time usage data can give administrators instant visibility of throughput and capacity for scale-up across an entire fleet of instruments, enabling more timely and effective decisions.
Improve budget forecasting and justification of capital requests – Usage data can provide important insights into which instruments are worth replacing, where new equipment could provide added value, and whether current assets are providing the expected return on investment.
De-risk operations and optimize service intervals – Usage and performance data is an important element of failure modes assessment to determine how often critical equipment requires preventative maintenance and what level of service coverage is most cost efficient.
“An investment in knowledge always pays the best interest.”
― Benjamin Franklin
Why isn’t evidence-based laboratory asset management the norm?
Given that the best decisions are data-driven, why is laboratory asset management still typically more of an art than a data-driven science? In the vast majority of cases, the problem arises not from lack of data, but rather from the difficulty of aggregating and analyzing the data. Most labs actually capture a significant amount of useful data in handwritten log books, laboratory notebooks, instrument log files, and service records. User ID, event details, run times, error logs and maintenance test results are all useful sources of information for trend analysis and troubleshooting.
However, manually recorded usage data may need to be collected from numerous logbooks around the lab, and there’s no guarantee that these records will be complete and accurate. Instrument log files are typically developed for service engineers only, with data in a form that is difficult and time consuming to extract, import and parse into a centralized database.
The situation can be even more unwieldy when managing a fleet of systems across multiple sites globally. In these cases, it is not unusual for the various labs to have different ways of working, incompatible information management systems, and varying degrees of diligence. Even in the best-case scenarios, the data may not be available in real-time, which can prevent rapid and responsive decision-making.
Making it better
Despite these challenges, advances in software and cloud technology promise to ease the burden of usage data aggregation and analysis, enabling lab managers to make better use of the wealth of historical data available, and to gain real-time insights into exactly how and when their instruments and consumables are being used.
Find out more about instrument management tools.
About the author
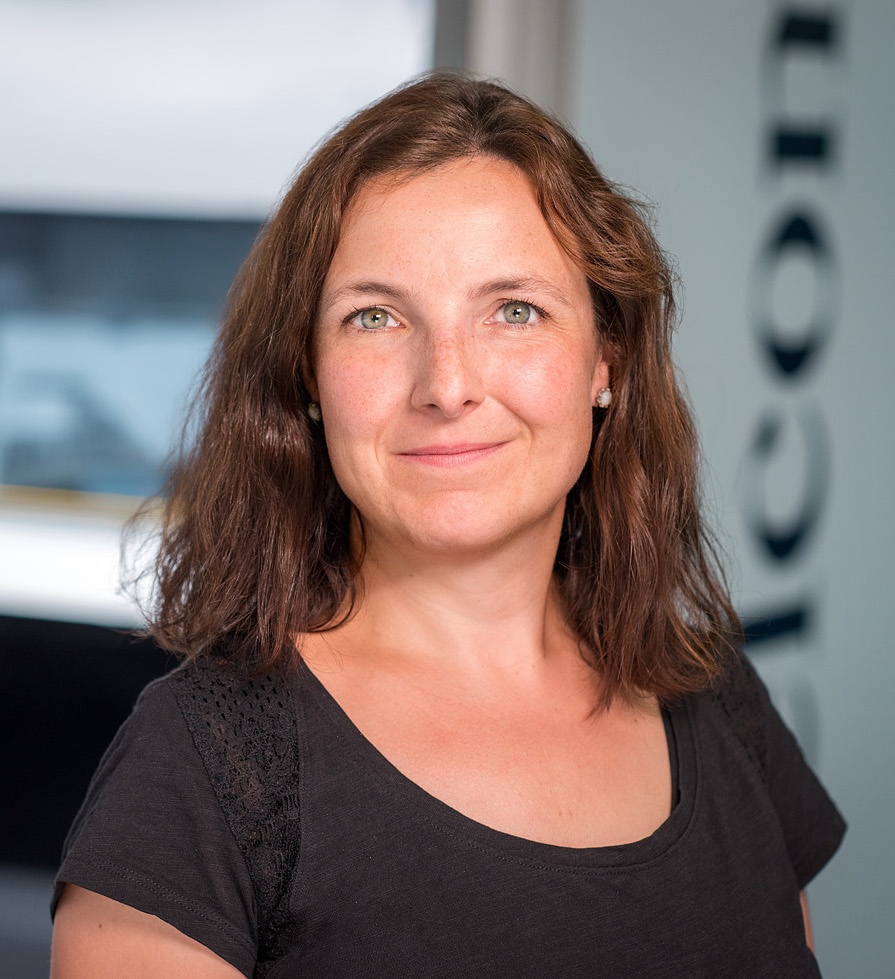
Michelle Aichele
Michelle is product manager at Tecan Switzerland and has a background in clinical diagnostics automation and product management. Before she joined Tecan she worked as a biomedical scientist with focus on immunoassays and hematology. This allowed her to gain experience in clinical laboratory automation and she became passionate on development automation workflows with Tecan instruments and software. She joined Tecan in 2007 and is now responsible for automation software product management.