By Michelle Aichele
Are you guilty of making decisions without the data to back them up? In today’s busy labs, mission-critical decisions about laboratory equipment purchases, service contract renewals, consumables spending, and staffing are often made on the basis of incomplete information. Having a clear picture of instrument usage and burn rates of associated reagents and consumables can help you uncover new ways to cut costs and improve performance in the laboratory. In the previous article we highlighted how crucial it can be for labs to monitor instrument utilization data. Now let’s consider more specifically what you can learn from analyzing all this data.
Get your business intelligence from instrument utilization data.
Maximize instrument uptime and increase throughput
Why did a particular instrument run fail? Why are some protocols less efficient than others – or have more workflow errors? Why do similar tasks take longer to complete at different times of the day, or on different days of the week? To optimize instrument uptime and increase throughput, you need to get to the root of such questions and identify underlying causes. Historical instrument usage patterns may highlight capacity gaps, help you deploy resources more effectively, and improve troubleshooting. Here are 5 types of insights that Tecan customers frequently come across when they analyze instrument utilization data.
1. Capacity gaps and unnecessary downtimes that are costing money
Having a consistent system in place to automatically extract and analyze data about instrument and consumables usage—both historically and in real-time—can give you insights into when, where and why instruments are being under-utilized. With the right analytics approach, you should be able to easily visualize the relevant data, and use these insights to fill capacity gaps and minimize downtime. Eliminating manual recording of usage data also ensures that you get a complete and accurate data set.
2. Hidden usage patterns that reveal root causes of productivity problems
When a particular shift shows lower performance on a regular basis, the reasons can vary. For example, instruments may have a greater tendency to fail after running non-stop for several hours; staff might be more tired at night and therefore less productive; or analysis runs may be delayed because the necessary consumables or samples are not arriving in the laboratory on time. If you have better visibility of when and how systems and consumables are being used, you can identify and trouble-shoot problems more effectively. Seemingly obvious solutions to increase productivity often turn out to be ineffective because they don’t address the root cause of the problem. To spot telltale patterns and unravel the true root causes, labs need a way to more easily visualize and analyze the available instrument utilization data.
One lab, for example, observed that there seemed to be lower sample testing output on Mondays. Initially they concluded that this was because more time was typically spent on Mondays preparing reagents for the week, reducing the time available for testing. However, when schedules were updated to address this problem, they found the pattern of low productivity on Mondays persisted. It wasn’t until the lab manager analyzed the instrument utilization data that the root cause became more apparent. As expected, the data showed that on some Mondays there were long downtimes at the beginning of the day before work started. However, on other Mondays this was not the case. The dates with the longer downtime gaps correlated with dates when weekly sample shipments hadn’t arrived on schedule. With this insight the lab manager was able to implement logistical changes to ensure samples were delivered on time, resulting in an instant productivity boost.
3. Error-prone or ambiguous methods that need to be updated
Instrument utilization data can also highlight when a particular method is confusing or more error-prone than it should be. For example, when a liquid handling protocol is not defined well enough, there might be considerable operator-dependent variations that increase the chances of error or variability in the results. Analysis can correlate instances of lower performance, errors or increased runtimes with specific methods. With these insights, you can pinpoint which protocols are likely to need better definition, and then monitor the results to determine whether any changes are having the desired effect.
4. Inefficient deployment of resources across labs or organizations
When managing resources deployed across multiple labs, it is important to have an accurate and timely overview of productivity, work loads, performance fluctuations, and overall quality. It is easy to lose sight of the big picture when operating many different instruments, or entire fleets, across multiple sites. In such cases, it pays to look for a solution that enables global data access, visualization and analytics. Better visibility of instrument and consumables usage across your entire fleet can improve transparency, help analysts compare system performance more easily, and enable more efficient deployment of resources.
5. Unmet training needs
When you spot trends showing that certain instrument operators consistently take longer to finish a task, or that some operators produce significantly more errors than others, it may be an indication that more training is needed, or that existing training methods are not effective. Usage data can help you spot these trends more quickly and make a more compelling argument for change. When addressing the performance of specific operators, sensitive data such as operators’ names can be anonymized, for example by using an alias or a hexadecimal code. This enables staff members to benefit from the insights without feeling named and shamed.
If we’d known then what we know now...
As these examples show, instrument utilization data is a valuable asset, provided you have the means to analyze and interpret it easily. Nowadays, with more devices connected to the cloud, we are generating more data than ever. To make the most of all this information, data aggregation and analytics must become easier and more intuitive for technicians, lab managers and operations directors – especially if you are operating a fleet of systems across multiple sites globally. Let’s be honest: if data analytics systems are clumsy and annoying to work with, we are less likely to find the time in our busy schedules to review the data and address the problems.
In upcoming articles we will look into what types of solutions are available to help lab managers get the most from instrument and consumables utilization data—including looking at the benefits of cloud-based data management, what can be done to ensure data security, and how more information about consumables usage can inform procurement planning.
To Learn more, visit our product site to watch a tutorial.
About the author
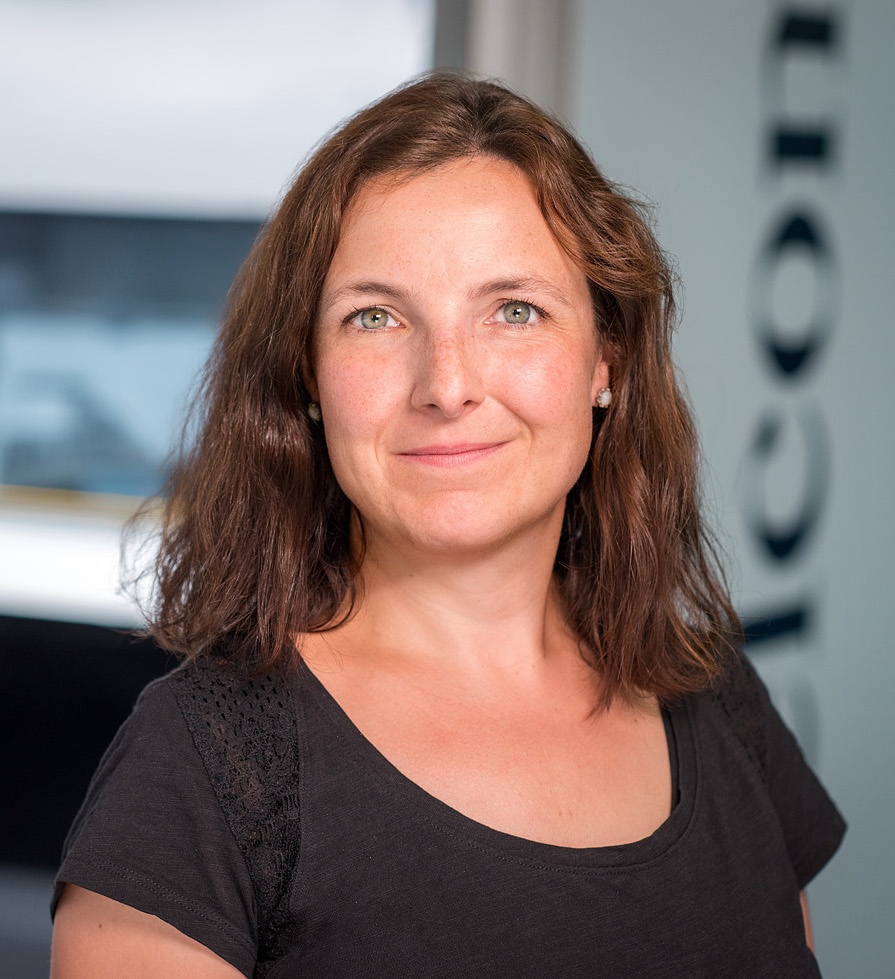
Michelle Aichele
Michelle is product manager at Tecan Switzerland and has a background in clinical diagnostics automation and product management. Before she joined Tecan she worked as a biomedical scientist with focus on immunoassays and hematology. This allowed her to gain experience in clinical laboratory automation and she became passionate on development automation workflows with Tecan instruments and software. She joined Tecan in 2007 and is now responsible for automation software product management.